Compounding technology for Rubber Compounds / Elastomers
Elastomers are the third most important group of plastics after thermoplastics and thermosets. Elastomers are dimensionally stable, but elastically deformable plastics, whose glass transition point is below room temperature. They can deform under tensile, shear and compressive load, but then return to their original undeformed shape.
Chemically, elastomers are macromolecules that are irreversibly connected to each other only by a few wide-meshed crosslinking bridges. With thermoplastic elastomers, these crosslinking bridges can be annealed under the influence of heat so that they exhibit a thermoplastic behaviour. Modifications in the rubber compounding technology can be used to produce elastomers with tailored hardness degrees, crosslinking densities and application temperatures.
Compounding requirements for Rubber Compounds / Elastomers
Excavations in Guatemala have shown that already in the 3rd century, the Maya knew rubber as a material. Since the 18th century, more and more applications are described. Invention of the vulcanization process by Charles Goodyear in 1839 enabled stable elastic properties both in cold and hot conditions, and thus the breakthrough to technical applications as well. At the beginning of the twentieth century, German chemists succeeded in producing synthetic rubbers.
Traditionally, elastomers have been produced on internal mixers or rolling mills. These established processes offer advantages such as maximum flexibility, precise offline dosing of even the smallest formulation proportions, as well as variable dwell and mixing times. However, limitations such as high specific energies, interim storage times and also property fluctuations between individual batches, have underlined the advantages of continuous processing in compounding machinery. These typically include uniform process conditions, narrow residence time distribution, integration of process steps and improved product quality consistency. The BUSS rubbercompounding technology and especially the BUSS Kneader can offer even more advantages with its precise temperature control, the ability to mix high proportions of filler in an excellent and yet gentle way, and also the ability to inject liquid ingredients such as softener oils or reagents directly into the process zone at the optimal position.
The widespread and highly successful use of the BUSS Kneader for silicone and fluoroelastomers has been known for decades. Recently, a wide range of other application fields has been added to the BUSS compounding technology. The integration of process steps, the expansion of requirement profiles and the use of alternative recipe components play the main roles.
Sophisticated processes are used to accommodate and implement these high standards. In the BUSS technical centre, processes can be developed, optimized, and the first scale-up steps realized with a throughput factor of 10. With the BUSS Kneader the compounding and pressure build-up stages can be directly flanged or decoupled so that they can be independently optimized. In the case of elastomers, pressure build-up is usually by a flange-mounted discharge extruder for pelletizing or further processing. The split barrel of the BUSS Kneader ensures fast access and high system availability. Together with broadly based BUSS compounding process expertise, the modular design and therefore adaptable arrangement of the entire compounding line makes the BUSS Kneader an excellent choice for compounding elastomers.
Typical compounding plant layout for Rubber Compounds
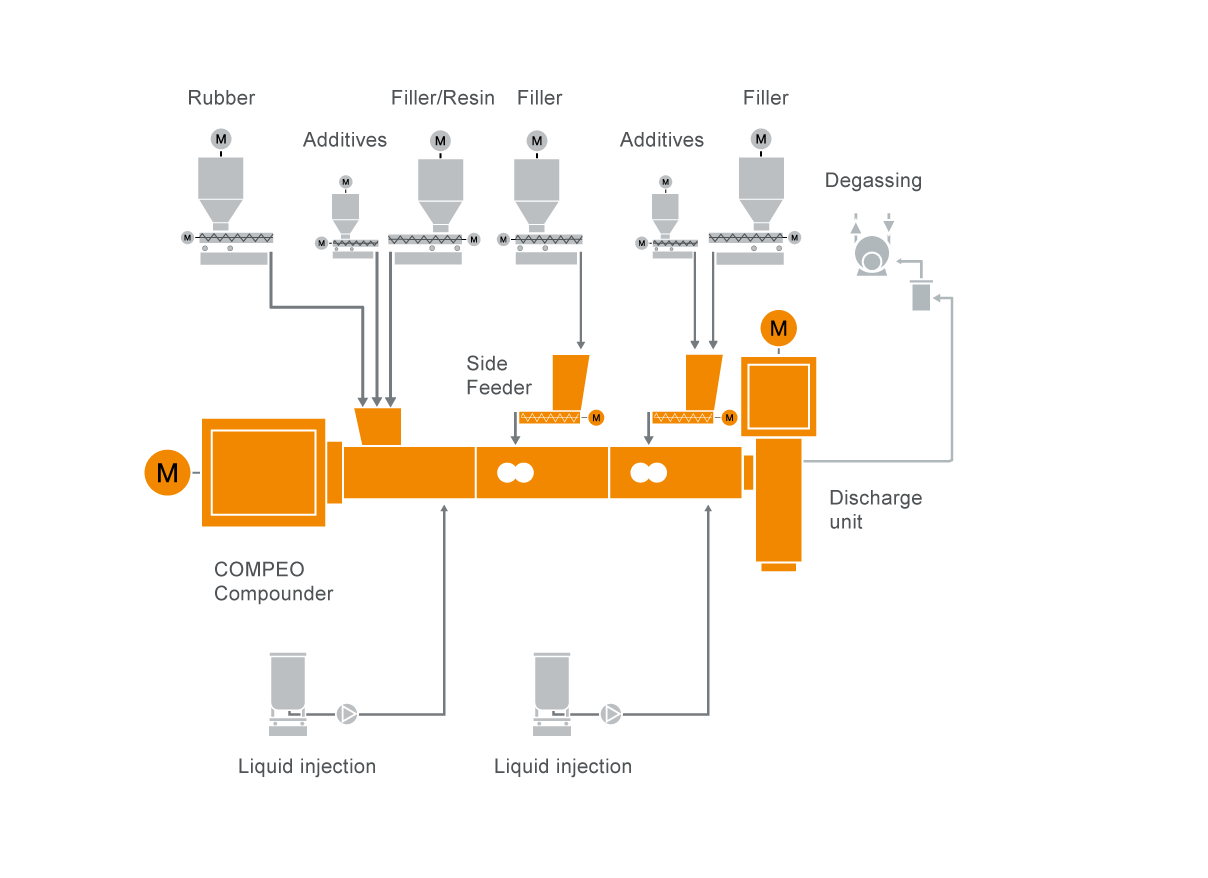
BUSS compounding systems offer the following specific benefits
Learn More
Downloads
-
COMPEO