PVC Cable Compounding Systems
Soft PVC cable insulation compounds
Depending on requirements, cable insulation mass by BUSS compunding systems utilizes various different plastics. They include polyolefin, TPE, PPE, EEFE, PVA, and of course soft PVC compounds. PVC has been used for cable insulation since 1932, originally as a replacement for rubber. Due to their relatively high dielectric strength, leading to corresponding induction losses and heating, soft PVC cable insulation compounds are only used at AC voltages of up to 10 kV. Most soft PVC cable mass applications are in this field. Formulations can be adjusted to customize the application temperature range, mechanical characteristics and flexibility of use, flammability and processing.
Here are two examples:
- Softener formulation adjustment can raise the continuous operating temperature limit to 105°C.
- Aluminium trihydroxide (ATH) additive can systematically reduce flammability and smoke formation. Regulatory authorities such as the VDE, EN or UL issue standardized property profiles for insulation and coating compounds.
Typical applications
The main application fields of cable insulation mass produced with PVC cable compounding systems by BUSS are power transmission up to the aforesaid 10 kV, domestic installations above all in private housing, and data transmission in general. The automobile industry almost exclusively uses soft PVC compounds.
Compounding requirements
PVC cable mass is usually compounded in two stages: hot/cold mixing in the powder phase, followed by compounding and pelletizing on a BUSS Kneader.
Compounding requirements can be summarized as follows. The plasticizers and other constituents like stabilizers, additives, fillers, reinforcements, flame retardants and others. are absorbed in the porous PVC grain and then must be systematically gelled, dispersively and distributively mixed, and agglomerated. This is all in compliance with well defined temperature limits. Custom-tailored property profiles lead to a wide variety of formulations, with efficient production in rather decreasing batch sizes.
The BUSS Kneader can make the most of its strengths profile at uniform, moderate and if necessary, adjustable shear rates. A range of output rates can be achieved on a given BUSS Kneader size according to the requirements of the customer.
In most cases all product variations can be covered with a universal shaft geometry designed to suit the formulations portfolio. Furthermore, the modularity of the entire system (shaft geometry, fittings, forming options, etc.) always enables adjustment to comply with different requirements. This is important for maximum security of investment.
With its low specific energy requirement for the most intensive mixing processes, simple volumetric scale-up, and maximum availability over a wide operating range, the BUSS Kneader within the BUSS PVC Cable Compounding Systems clearly remains a good choice for compounding PVC cable mass.
Typical plant layout for PVC cable compounding systems
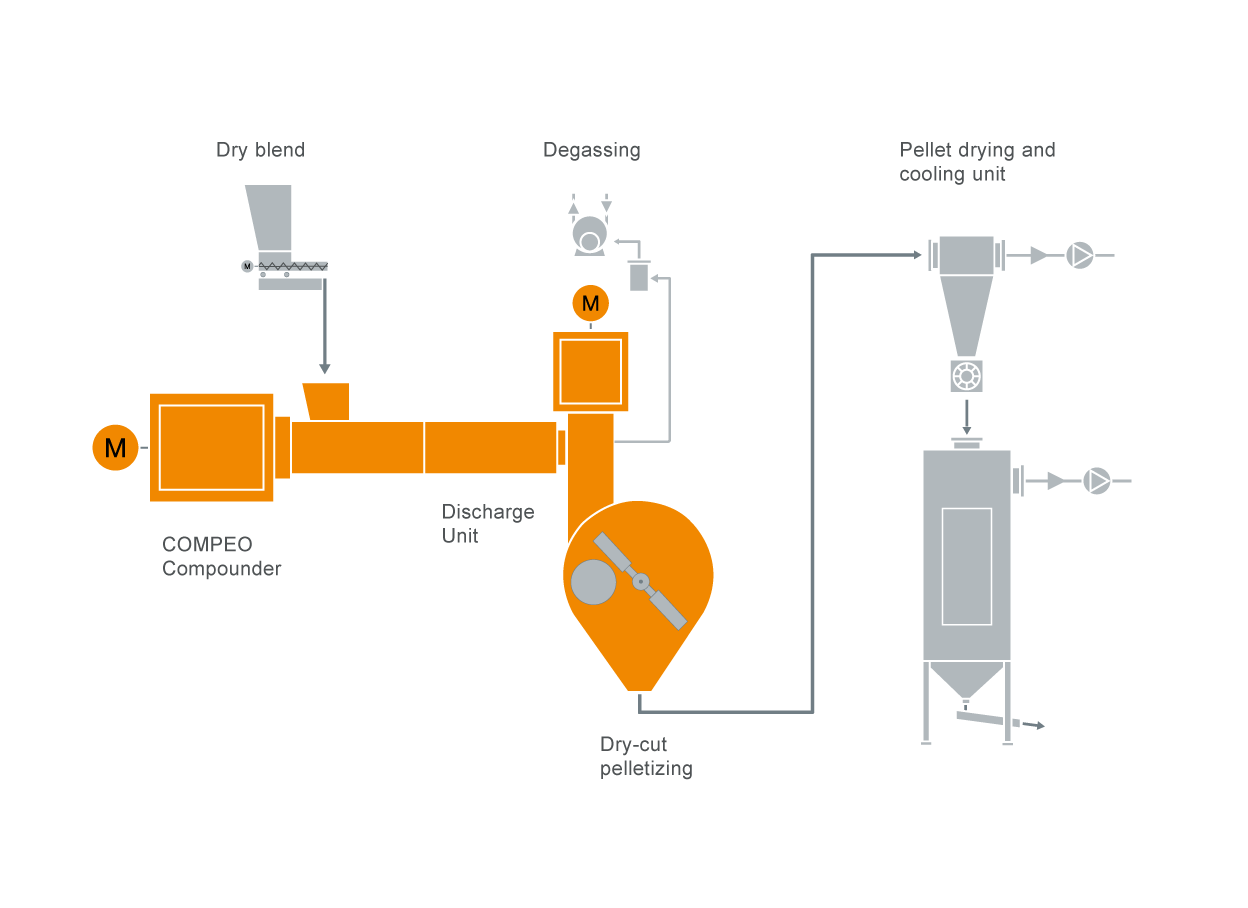
BUSS PVC cable compounding systems offer the following specific benefits
Learn More
Downloads
-
COMPEO