Compounding Sytems for Bioplastics
Bioplastics have been known for a long time. Their industrial production started in 1869, first based on cellulose, and then on casein in large quantities as artificial horn in the early twentieth century. With the technical breakthrough soon afterwards to petroleum-based plastics, with production at much lower cost, bioplastics were no longer produced. It was not until decades later, in the 1980s, that rising crude oil prices and gradually changing ecological awareness led to interesting new developments in the field of bioplastics. And thus also to new compounding systems for production.
The terms bioplastics or biopolymers are still not used consistently. However, they mostly include a large number of different plastics that fulfil at least one of two criteria:
- Bioplastics comprise at least a proportion of renewable (vegetable) raw materials. Almost all bioplastics are bio-based.
- Bioplastics are biodegradable, i.e. they can be degraded by naturally occurring microorganisms into water and CO2 with a small proportion of biomass. Bioplastics from fossil raw materials can also be biodegradable.
Bioplastics are defined by these two properties either on their own, or together: bioplastics are bio-based, biodegradable, or both. Conventional plastics do not meet any of these criteria. Biogenic raw materials or naturally occurring biological macromolecules such as proteins, as well as natural fibre-filled or reinforced materials (see also separate article) are therefore not included.
Typical applications
The main applications of bioplastics are packaging, consumer durables, and technical parts in the transport and construction industries.
Compounding requirements for bioplastics
To ensure the desired properties, bioplastics compounding systems demand excellent dispersive and distributive mixing at moderate shear rates and low product temperatures.
The careful incorporation of fibres, fillers and additives often requires multiple metering of dry ingredient streams and possibly also the injection of liquid additives at defined positions in the compounding machinery.
The BUSS Kneader’s specific capabilities are outstandingly suitable for such applications. Thanks to its operating principle, the enormous number of mixing cycles at moderate and adjustable shear rates enables the highest possible mixing efficiency over short processing lengths with narrow residence time spectra. The BUSS Kneader’s two-stage system systematically separates the compounding and pressure build-up stages so that each of them can be independently optimized.
The split barrel of the BUSS Kneader and the retractable casing of the discharge extruder ensure fast and easy access to the processing components for high system availability.
Together with broadly based BUSS process expertise in compounding, the modular design and therefore adaptable arrangement of the entire compounding line, make the BUSS Kneader is first choice for compounding technical bioplastics.
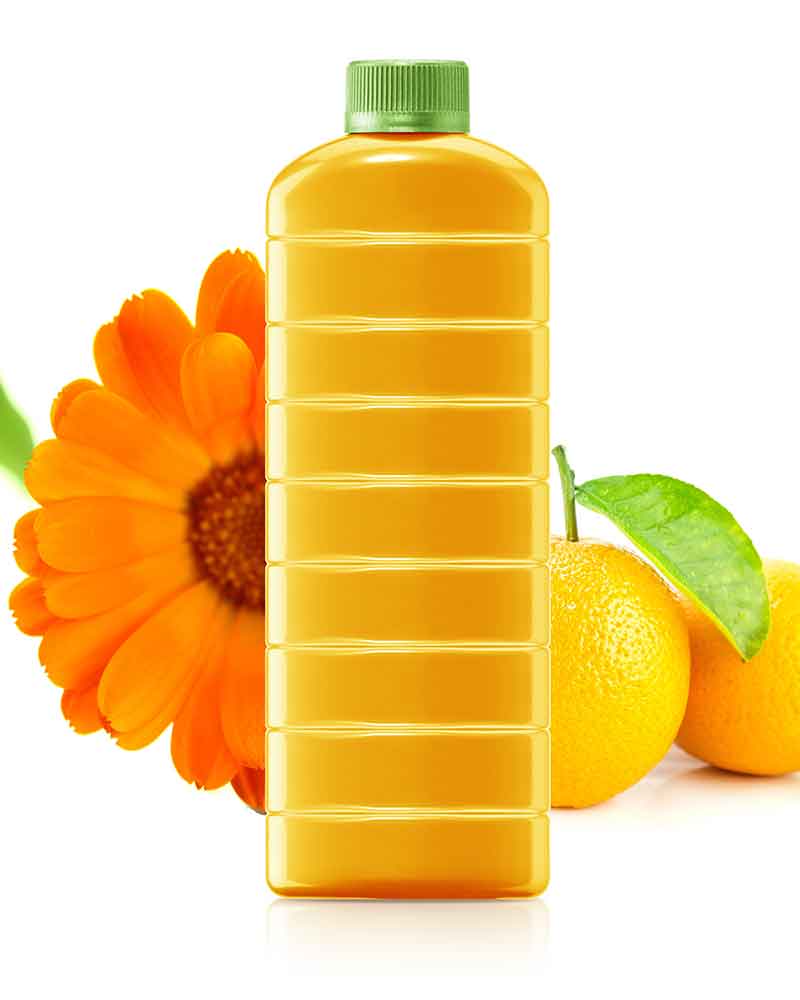
Typical plant layout for compounding bioplastics
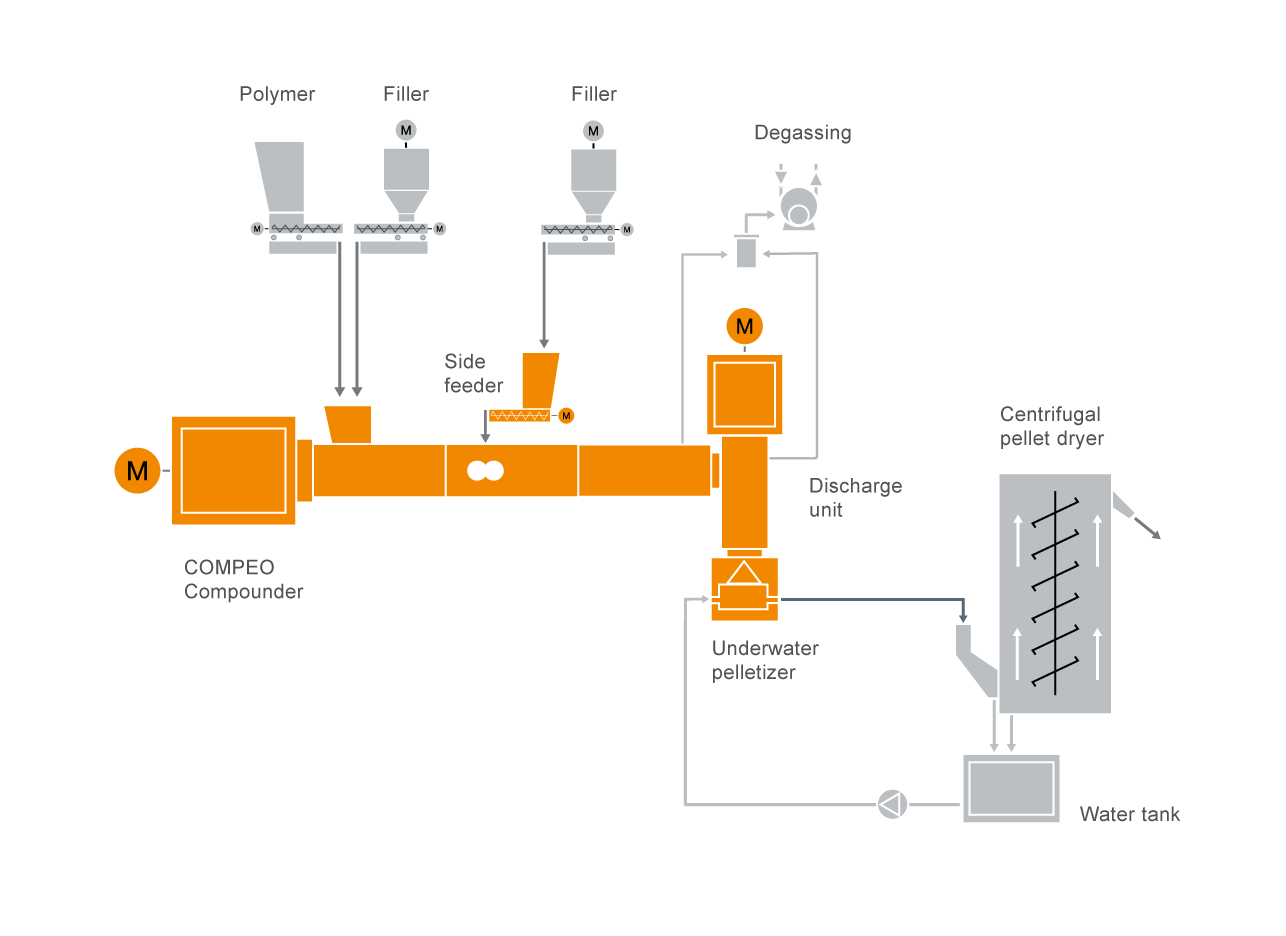
BUSS compounding systems offer the following specific benefits
Learn More
Downloads
-
COMPEO
-
Laboratory Kneader MX 30