In times of lockdowns, limited flight connections, and restrictive entry regulations, the service call of a Korean customer reached us. Our customer produces calendered PVC films for medical packaging and suddenly had metallic contamination in the compound. First, we tried to find and fix the problem together through video-supported analysis and troubleshooting. But the problem was not simple to fix remotely. On the other hand, a machine failure in the current situation and with a product that was urgently needed was just as unacceptable for the BUSS service team.
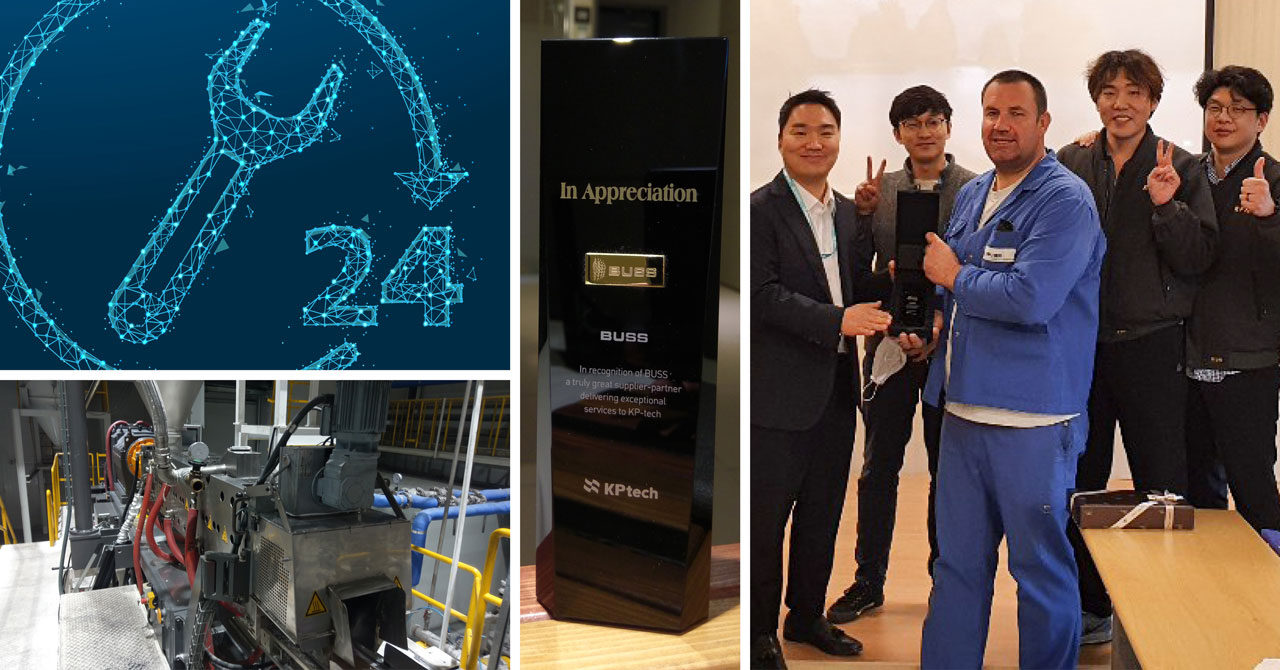
Without further ado, one of our service technicians agreed to fly to Korea as quickly as possible — provided that all safety measures would be complied with. The quickest route was via Tokyo to Seoul. Once in Seoul, our BUSS colleague was tested for COVID-19 and had to be quarantined for 24 hours in a Korean officers’ barracks. The negative test result allowed our colleague to journey onward to the customer.
After 48 hours, the operation at the Korean compounding plant began. After a short on-site analysis and some testing, the source of the contamination was quickly discovered. With a few targeted measures, our colleague was able to get a grip on the problem. Owing to the targeted replacement of suitable original process parts and technical advice, the situation could be corrected rapidly. The compounding plant was functional again on the same day and is again now producing calendered PVC films for medical packaging in the usual manner.
How our BUSS service technician will return to Switzerland is now the next and bigger challenge. For our Korean customer and for us, he is definitely one of the heroes of everyday life.
#stayhealthy #staysafe